Los pisos de concreto son la opción más popular para la disposición de edificios residenciales e industriales. Con el tiempo, el material pierde su resistencia bajo tensión constante. Se forman grietas de deformación y depresiones en la superficie. Para proteger la base de daños y prolongar su vida útil, se utilizan impregnaciones o acabados para pisos de concreto. Puede aprender sobre las características, tipos y métodos de aplicación de las composiciones del artículo.

Para aumentar la resistencia del revestimiento y hacerlo invulnerable a factores externos agresivos, se permitirá el acabado de un piso de concreto.
Contenido
- 1 ¿Qué son los suelos de hormigón con una capa superior endurecida?
- 2 Variedades de impregnación para piso de concreto.
- 3 Características de las impregnaciones de polímeros para suelos de hormigón.
- 4 Tecnología de impregnación a base de hormigón
- 5 Topping: esta es una forma moderna de fortalecer una base de concreto
- 6 Ventajas distintivas de la cobertura de hormigón
- 7 Áreas de uso del piso de cobertura
- 8 Tecnología de acabado de suelos
- 9 Características de la disposición de la cobertura en pisos de concreto.
- 10 Cómo hacer un piso de concreto con un endurecedor: método seco de aplicación de la composición
¿Qué son los suelos de hormigón con una capa superior endurecida?
La regla para pisos de concreto se usa ampliamente en varias instalaciones. Esto se debe a las altas cualidades técnicas y operativas del recubrimiento, que se caracteriza por una tecnología de instalación simple, confiabilidad, durabilidad y costo asequible. Sin embargo, el piso experimenta constantemente diversas cargas que contribuyen a la destrucción del hormigón. No solo la humedad penetra en su estructura, sino también los productos químicos que filtran el revestimiento.
Para aumentar la resistencia del piso y extender el período de su operación, existen medios especiales en forma de impregnaciones y coberturas. Estos endurecedores penetran en la estructura porosa del hormigón, bloqueando los poros. Esta protección aumenta la resistencia y durabilidad del revestimiento, que puede soportar tensiones y tensiones más intensas. Al mismo tiempo, el piso de concreto está sellado, por lo que la humedad y los elementos químicos no pueden penetrar en su espesor.
La destrucción gradual del pavimento de hormigón va acompañada de la formación de partículas finas. El endurecedor contribuye a la eliminación fiable del polvo de la superficie. Las sales en su composición se unen, obstruyendo las vías de formación y eliminación de polvo. Quitar el polvo de la superficie le confiere propiedades higiénicas, lo que es especialmente importante para los niños y las instituciones médicas.
Los pisos de hormigón con una capa superior reforzada, que se forma por impregnación o cobertura, tienen un aspecto estético.Esto se consigue gracias a una superficie plana y lisa que se puede teñir de cualquier color. Puede usar un piso de concreto de este tipo en una casa privada, taller de producción o área pública.
¡Importante! Para garantizar una protección confiable de los pisos de concreto mediante impregnaciones y coberturas, es importante observar estrictamente la tecnología de aplicación del endurecedor a la superficie.
Variedades de impregnación para piso de concreto.
La impregnación para base de hormigón es una composición líquida que tiene una base orgánica o inorgánica. La última opción se utiliza principalmente. Tales impregnaciones minerales contienen compuestos de potasio y sodio, que penetran profundamente en la estructura del hormigón, provocando reacciones químicas en su capa superior. Esto contribuye a la neutralización de los componentes libres con la creación de enlaces vítreos insolubles cristalinos adicionales, que proporcionan endurecimiento de la superficie.
Impregnaciones minerales modernas para suelos de hormigón para el control del polvo y los refuerzos están basados en polisilicato de litio. Penetran en los poros más pequeños. El período de procesos químicos es de 10 a 12 días. Basta con procesar la superficie una vez sin frotar y lavar el piso.
Las impregnaciones orgánicas de refuerzo y desempolvado para pisos de concreto son acrílicas, poliuretánicas y epoxi. La primera opción, a base de agua, es aconsejable para sustratos que no aceptan cargas pesadas, así como para soleras destinadas a pavimentos. La composición se puede utilizar para hormigones de grado no inferior a 200. Una superficie de hormigón con impregnación acrílica tendrá cualidades hidrófobas. Es capaz de soportar una alta humedad, lo que garantiza una alta higiene.
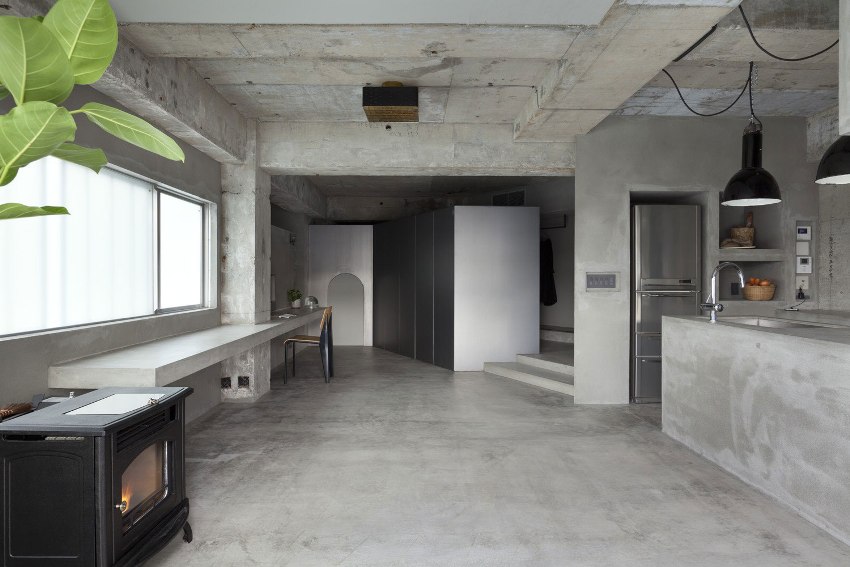
La mezcla contiene muchos componentes diferentes, entre los que se encuentran plastificantes, fijadores, colorantes.
Características de las impregnaciones de polímeros para suelos de hormigón.
Las impregnaciones de pisos de concreto epoxi son las más confiables y duraderas. Están representados por composiciones acuosas de dos componentes a base de resinas epoxi. Se recomienda instalar tales impregnaciones en tiendas de procesamiento de alimentos, refrigeradores y congeladores, y en instalaciones médicas. La principal desventaja de las formulaciones es su alto costo.
El más popular es la impregnación de refuerzo para pisos de hormigón "Epoxol", que se puede utilizar para locales residenciales, públicos, industriales y de almacén. El endurecedor contiene disolventes orgánicos, resina modificada con organosilicio y aditivos funcionales.
La impregnación de poliuretano es la más extendida. Le da a la base cualidades adicionales de repelencia al agua, es más versátil y duradera. Esta composición se puede utilizar para hormigón de baja calidad. Después de la aplicación, el piso se convierte en un polímero de concreto, que se caracteriza por su resistencia al impacto, propiedades libres de polvo y a prueba de humedad. La principal desventaja es el fuerte olor, que se evapora una vez finalizado el proceso de polimerización.
¡Importante! El más justificado es el uso de impregnación a base de poliuretano para pisos de concreto en el garaje.
La composición más popular es Protexil. La impregnación para suelos de hormigón y hormigón está especialmente diseñada para superficies de suelos industriales que soportan un transporte importante, cargas mecánicas y están bajo la influencia de un entorno agresivo. La composición se puede utilizar tanto para suelos nuevos como antiguos.
Tecnología de impregnación a base de hormigón
El primer paso es preparar la base antes de aplicar la impregnación de poliuretano o epoxi al piso de concreto. El proceso se realiza con la ayuda de una máquina de pulir, que elimina la capa superior suelta, la lechada de cemento, los restos de aceites y suciedad. El procedimiento es necesario para abrir los poros del hormigón y asegurar la penetración de la composición profundamente en el material.
Dependiendo del tipo de impregnación, la composición penetra en el hormigón de 2 a 8 mm, aumentando varias veces la resistencia de su marca.
Para aplicar la impregnación, utilice una brocha, rodillo o spray de aire. La composición se vierte sobre la superficie preparada en tiras y se distribuye con un cepillo, una escobilla de goma o un acondicionador de invierno sintético con una siesta larga. La impregnación debe ocupar uniformemente toda el área superficial, excluyendo la formación de charcos y lugares donde la composición se absorbe rápidamente en el concreto.
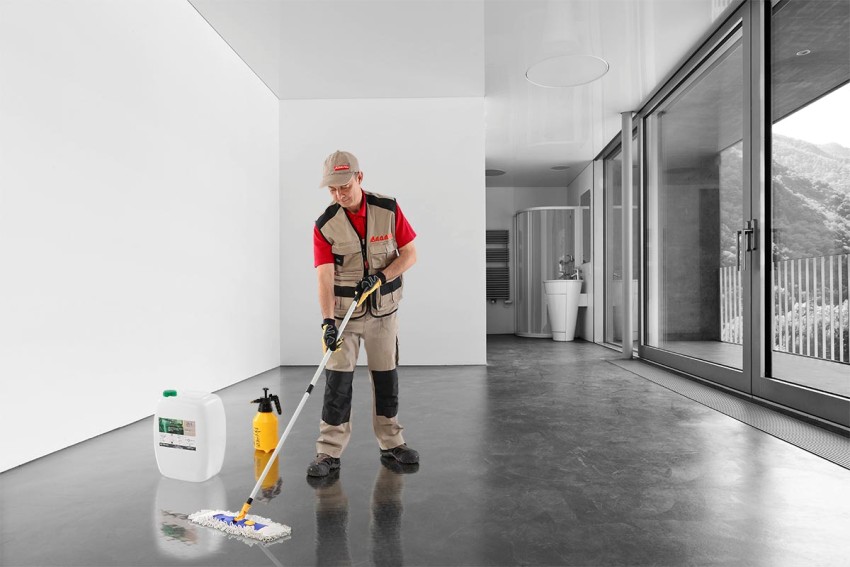
La cobertura se aplica como capa superior al concreto premezclado, creando así una protección de superficie confiable
La tecnología para aplicar compuestos orgánicos es algo diferente. Tal impregnación para un piso de concreto del polvo se aplica en varias capas. El primero debe reposar durante 40-60 minutos. A continuación, se aplica una segunda capa, después de 20 minutos, se debe eliminar todo el exceso de composición con una escobilla de goma o un trapo.
Topping: este forma moderna de fortalecer la base de hormigón
Topping: ¿qué es? El primer paso es aprender más sobre esta capa protectora. Este endurecedor de hormigón está representado por una superficie exterior duradera, que incluye cemento, aditivos plastificantes, fijadores y colorantes. El primer elemento actúa como enlace entre los áridos, evitando la delaminación del material.
El resto de ingredientes confieren al recubrimiento durabilidad, resistencia al impacto, resistencia al agrietamiento, resistencia a ambientes químicos agresivos, resistencia a las heladas, cualidades higiénicas, reflectantes, antiestáticas y decorativas.
La cobertura está disponible en estado líquido y seco. La primera opción incluye compuestos inorgánicos que se disuelven bien en agua. Durante la aplicación de la mezcla al revestimiento del piso, el compuesto penetra en los poros del concreto, formando sellos duraderos que son resistentes a la humedad. La cobertura seca tiene un estado pulverulento. En forma de pequeñas migas, la composición se desmorona hacia la superficie, seguida de apisonamiento y trituración. Esta opción tiene un costo menor.
¡Importante! El uso de material seco implica la formación de costuras en la superficie.
Ventajas distintivas de la cobertura de hormigón
Este método de fortalecer la base de hormigón ha reemplazado hierro, cuando, al instalar pisos de concreto, se esparció cemento seco sobre la regla en una capa delgada, seguido de llana. La cobertura en forma de mezcla seca o líquida se aplica a una regla fresca o endurecida, que luego se procesa mediante máquinas rectificadoras. Gracias a los aditivos especiales, la superficie tiene una estructura mejorada y el relleno de grano fino le da textura.
Este tipo de revestimiento protector no permite que pase la humedad. Topping penetra profundamente en la estructura porosa del hormigón, sellando sus poros. La superficie no necesita un mantenimiento especial. Gracias al acabado, se prolonga la vida útil del suelo de hormigón. Este endurecedor también se caracteriza por un coste aceptable. Además, al organizar un piso de concreto, puede usar cemento de baja calidad, que se compensa con una capa protectora ultrarresistente.
El recubrimiento final muestra una mayor susceptibilidad a ciertos componentes químicos, lo que contribuye a una disminución del rendimiento de la superficie. Un piso así no se puede reparar. Si es necesario, la superficie se desmonta y se coloca una nueva base.Sin embargo, debe tenerse en cuenta que el período de funcionamiento del piso es de al menos 15 años, durante los cuales mantendrá sus cualidades operativas y decorativas.
Áreas de uso del piso de cobertura
Esta tecnología para fortalecer una base de hormigón se utiliza en almacenes, talleres industriales y de producción. Por su higiene, estos suelos son indispensables en la industria alimentaria. Debido a su resistencia a las heladas, los pisos de concreto con cobertura son la mejor solución para refrigeradores y congeladores. La presencia de cualidades reflectantes asegura la demanda del endurecedor en objetos con temperaturas elevadas.
Las cualidades de alta resistencia al desgaste hacen que el revestimiento protector sea indispensable en lugares con mayor vibración y estrés mecánico, como estacionamientos, centros comerciales y de entretenimiento, instituciones médicas, culturales y educativas, áreas peatonales con alto tráfico. Una regla de piso industrial de este tipo se usa ampliamente en concesionarios de automóviles, garajes, hangares, garajes, donde el revestimiento de concreto superior está en contacto constante con gasolina y combustible diesel, líquidos ligeramente alcalinos y aceites minerales.
¡Importante! La cobertura no se puede utilizar en locales donde se utilizan ampliamente ácidos y álcalis, para los que se aceptan impregnaciones especiales.
Topping ayuda a aumentar la vida útil de los suelos de gimnasios, campos deportivos y piscinas. El recubrimiento se usa ampliamente hoy en día en instalaciones civiles, lo que se asocia con un cuidado poco exigente, durabilidad y superficie decorativa cuando se usan compuestos coloreados.
Revestimiento de piso de concreto: variedades de endurecedores
Hay tres tipos de endurecedor de hormigón: cuarzo, corindón y metalizado. La primera opción es la más popular y demandada. También tiene el costo más asequible. El relleno principal de la mezcla es la perlita, que se puede combinar con pigmentos colorantes. Esta característica tiene un efecto positivo en las características técnicas y operativas de la superficie, cambiando su apariencia.
La cobertura de cuarzo es la mejor opción para sustratos que experimentan un estrés moderado, que es típico de almacenes, centros comerciales y de entretenimiento, instituciones educativas. Dichos endurecedores también se utilizan ampliamente en la construcción de edificios residenciales.
¡Importante! La capa de cuarzo ayuda a aumentar la resistencia del hormigón en 1,5 veces.
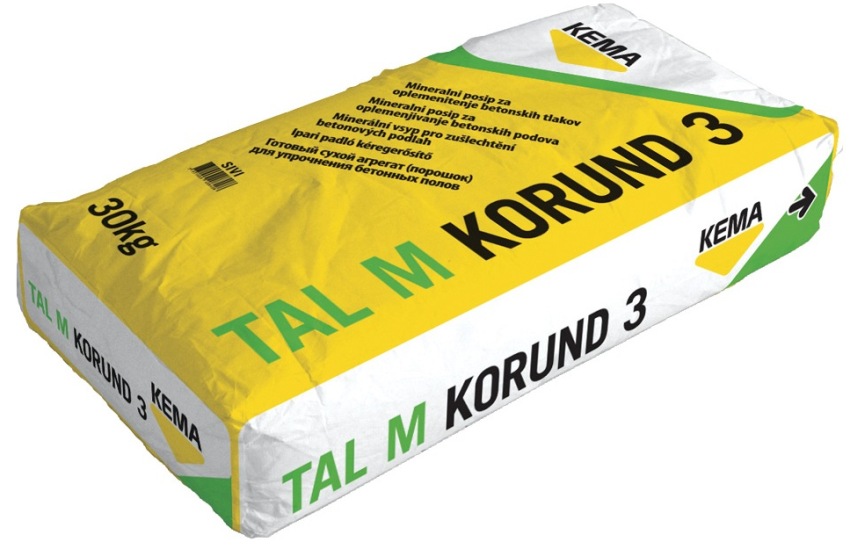
El relleno de corindón se selecciona para objetos en los que el piso está sometido a una tensión severa
En las coberturas de corindón, las virutas de corindón actúan como relleno. Este aditivo mineral tiene características de alta resistencia, mayor resistencia al desgaste y resistencia a la abrasión. El endurecedor aumenta 2 veces la resistencia del hormigón.
Artículo relacionado:
Una descripción detallada del trabajo preparatorio, características tecnológicas. Instalación de suelo radiante bajo tarima flotante.
Las coberturas de corindón se utilizan en instalaciones con equipos grandes y pesados instalados, así como en lugares con mucho tráfico de personas y vehículos. Un entorno de este tipo es típico de los locales tipo almacén, gimnasios, instalaciones para fines especiales y terrenos.
¡Importante! La capa de corindón le da a la superficie de acabado un agradable acabado mate.
El relleno principal de las coberturas metalizadas, cuyo precio es el más alto entre los análogos, son las virutas de metal. Tales mezclas contienen mortero de hormigón en su composición.Gracias a sus componentes, la cubierta metalizada se considera el refuerzo de piso más confiable, lo que aumenta su resistencia en 2,5 veces.
Dicha cobertura se usa para objetos que experimentan cargas excesivas, donde se instalan equipos masivos, se mueven equipos pesados a diario, que se caracterizan por una mayor vibración.
En la construcción de edificios residenciales, dicha composición no es práctica de usar debido al alto costo y la tecnología de aplicación bastante complicada.
Tecnología de acabado de suelos
Existen varias tecnologías para el acabado de suelos. El método DTW implica la aplicación de un endurecedor seco sobre una base de hormigón húmedo, que se puede rociar a mano o con carros especiales. Dichos mecanismos proporcionan una cobertura uniforme de una gran superficie del polvo. La base de hormigón se seca y se adhiere junto con la capa superior, lo que garantiza una alta adherencia.
Después de que la superficie se haya secado por completo, la mezcla absorbida se frota con una rectificadora especial. Dicho recubrimiento se distingue por su confiabilidad, resistencia, resistencia a varios factores adversos y durabilidad.
La tecnología WTW implica la aplicación de cobertura líquida inmediatamente después de colocar el piso de concreto. Esta opción de colocar el endurecedor se ha utilizado recientemente y aún no goza de popularidad, ya que el proceso de aplicación es bastante complicado, laborioso y caro. Sin embargo, dicho revestimiento se caracteriza por una máxima durabilidad y un alto efecto decorativo. La superficie es perfectamente plana, lisa, de color uniforme y hermosa.
El método WTD implica el uso de una capa final seca, que se coloca sobre una regla húmeda o seca. La etapa final del trabajo es un completo rejuntado de la superficie.
Existe una opción volumétrica para la aplicación de acabado, que proporciona el endurecimiento de la superficie del hormigón en todo el espesor. En la etapa de vertido de pisos de concreto, se mezcla un plastificante especial en la solución de trabajo, por lo que aumenta el rendimiento de la superficie.
¡Importante! El método volumétrico de aplicación de acabado implica el uso de hormigón de grado cemento para una regla no inferior a 350 para una base de hormigón.
Características de la disposición de la cobertura en pisos de concreto.
El espesor de la regla que se vierte se tiene en cuenta sin falta. Si se coloca sobre una base de hormigón vieja, su altura debe ser de hasta 70 mm. Si la capa final se aplica a un sustrato nuevo, el espesor de la regla alcanza aproximadamente 120 mm.
¡Importante! El nivel de las gotas superficiales debe estar dentro de los 4-5 cm.
Los trabajos de cobertura de bricolaje se realizan a una temperatura ambiente de al menos + 10 ° С. Si el clima es más frío, vale la pena organizar un calentamiento adicional de la habitación.
El topping es una tecnología compleja de tratamiento de superficies de hormigón, por lo tanto, para obtener un buen resultado, el proceso debe realizarse en una secuencia estricta. Los endurecedores de hormigón están disponibles en dos estados: líquido y seco. Cada opción se caracteriza por una tecnología individual para aplicar la composición.
La lechada se puede aplicar tanto a soleras nuevas como antiguas. El efecto será el mismo. El proceso se lleva a cabo en la siguiente secuencia.
El primer paso es preparar la base de hormigón. El revestimiento viejo se limpia a fondo de suciedad, escombros y polvo. En caso de grietas y baches, se deben rellenar con mortero de reparación de cemento u hormigón. La regla fresca debe lijarse.
La cobertura líquida se aplica con un rodillo o spray al sustrato preparado. Es necesario controlar cuidadosamente la absorción de la composición, que depende de la calidad de la superficie del hormigón. Si el proceso es rápido, se vuelve a aplicar la cobertura. El espesor del revestimiento es de 2-3 mm. El consumo de mezcla alcanza los 4-5 l / m².
La cobertura líquida se caracteriza por su versatilidad y rápida velocidad de fraguado. Sin embargo, tal composición tiene un costo más alto en comparación con la mezcla seca.
Cómo hacer un piso de concreto con endurecedor: método seco de aplicación de la composición
Las formulaciones secas se pueden adquirir en sacos de 25 y 50 kg. La mezcla se aplica sobre una regla de hormigón fresco 6-7 horas después de su colocación, si la superficie se ha endurecido a un estado en el que quedan huellas superficiales.
¡Consejo útil! Para colocar cobertura en áreas grandes, no es práctico e ineficaz utilizar el método manual; para esto, se utilizan máquinas rectificadoras especiales equipadas con un disco de trabajo grande.
Los trabajos de cobertura en seco se llevan a cabo en la siguiente secuencia.
En la primera etapa, un piso de concreto industrial se alisa con una amoladora. El procedimiento se realiza con el objetivo de nivelar la superficie hasta que esté completamente fraguada. Con la ayuda de un carro de cobertura, el 65% de la cantidad total de la mezcla se distribuye uniformemente sobre la base de hormigón desde las ventanas hacia la salida. El polvo comienza a absorber la humedad de inmediato. Se produce la reacción de cristalización de la composición, acompañada de un oscurecimiento gradual de la composición.
Cuando la superficie esté uniformemente oscura, es hora de aplicar lechada con la máquina. El proceso es necesario para nivelar la base y llenar el piso industrial con cobertura. Después de terminar el proceso de frotar en la mezcla, debe esperar hasta que la superficie se agarre. Esto se evidenciará mediante una impresión con una profundidad de 1 mm.
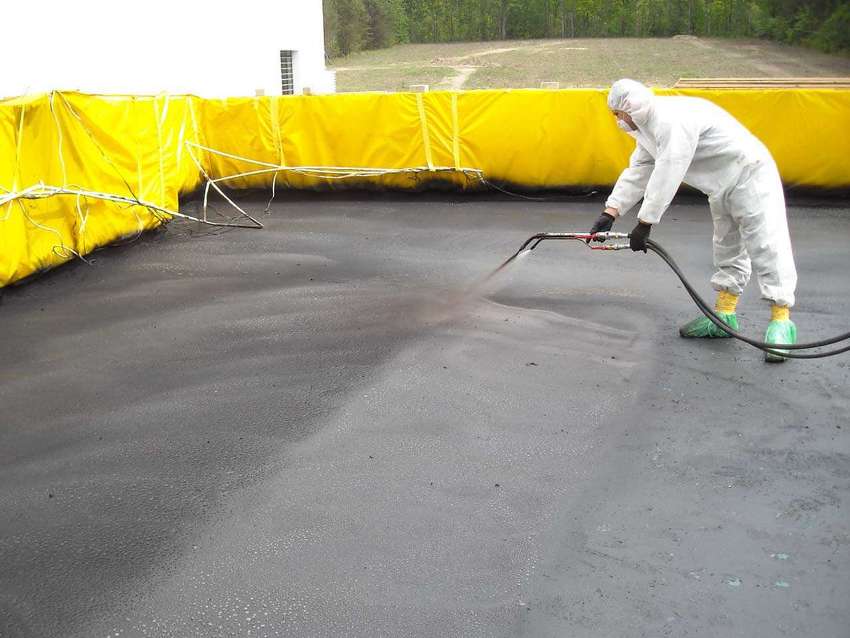
La mezcla de endurecimiento se aplica a la regla de hormigón fresco 6-7 horas después de su colocación.
Además, la mezcla restante se distribuye uniformemente sobre la superficie. Después de 24-48 horas, la base endurecida debe limpiarse con cuchillos. El proceso se lleva a cabo en 2-3 pasos hasta obtener una superficie de espejo.
¡Importante! El consumo medio de cobertura es de 4,5-5 kg / m².
La base terminada se cubre con curado, una solución que forma una película delgada que evita que la humedad se evapore del concreto durante la hidratación de la superficie. El curado se puede aplicar con spray o rodillo. Finalmente, se deben cortar las juntas de expansión. Evitarán que la superficie del hormigón se agriete durante el endurecimiento y retracción de la base, que estará completamente acabada a los 28 días. Las costuras deben rellenarse con sellador.
Cuando se utilizan suelos de hormigón como revestimiento completo, es recomendable reforzar la base con impregnaciones o coberturas. Tales composiciones aumentan las características de resistencia de la superficie, proporcionando resistencia al impacto, resistencia al desgaste, resistencia al estrés, la humedad y los productos químicos, y durabilidad del suelo.